
LATEST FOCUS | Multiple cooling and energy savings
IECI
Temperature control units for die-casting mould
IECI was founded in 1972 as an electro-hydraulic plant engineering company and later specialised, from the 1980s onwards, in the production of mould temperature controllers.
Today IECI is a leading manufacturer of die-casting temperature control systems and is present in 4 continents with a technical and sales support network in over 30 countries.
Continuous technological research has led IECI to develop special temperature controllers dedicated to injection groups (plunger and shot sleeve), core cooling machines, multi-channel cooling systems and quenching tanks.
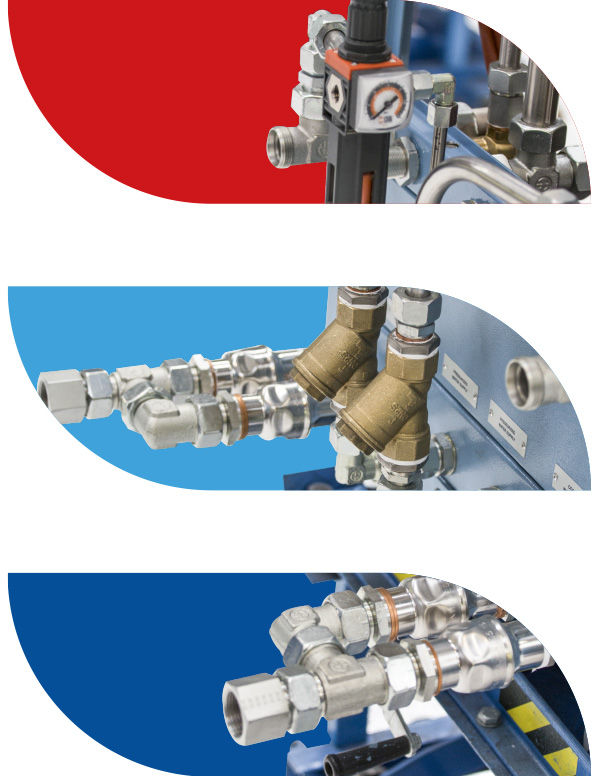
IECI products
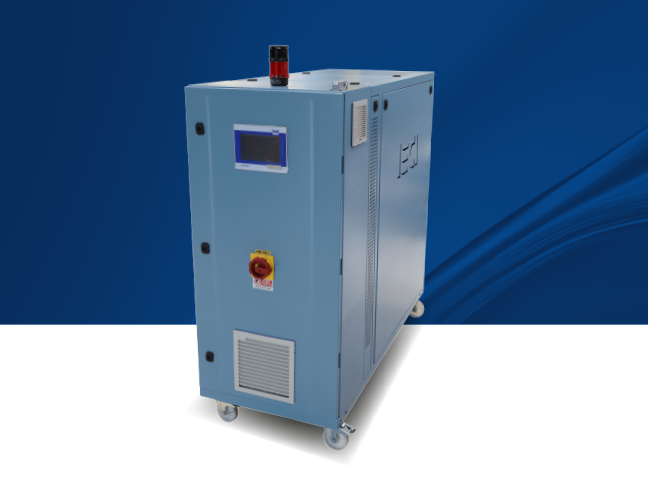
Water temperature control units
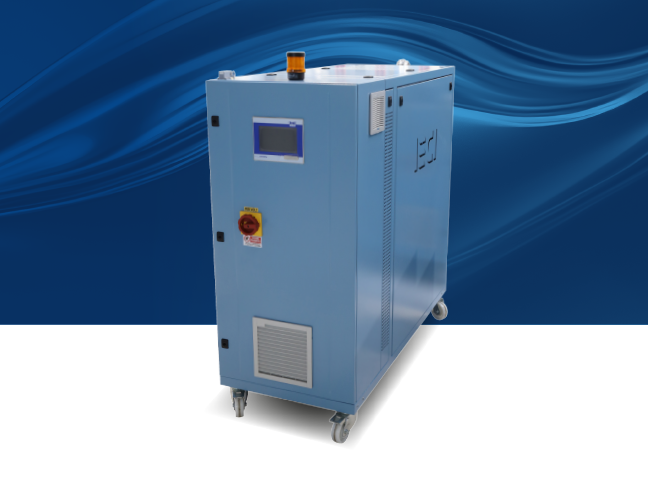
Oil temperature control units
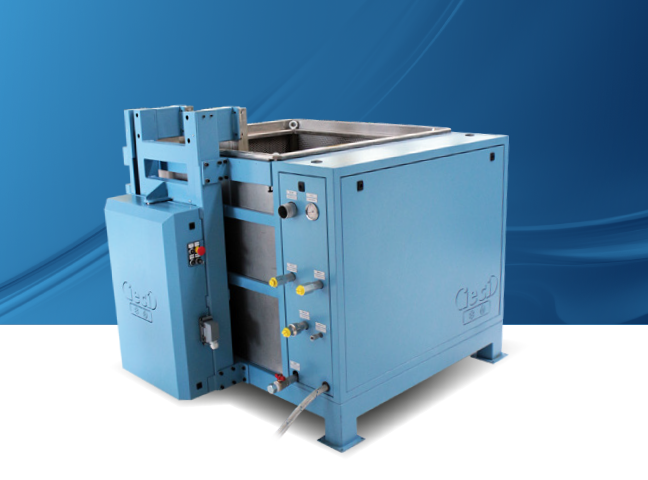
Quenching Tanks
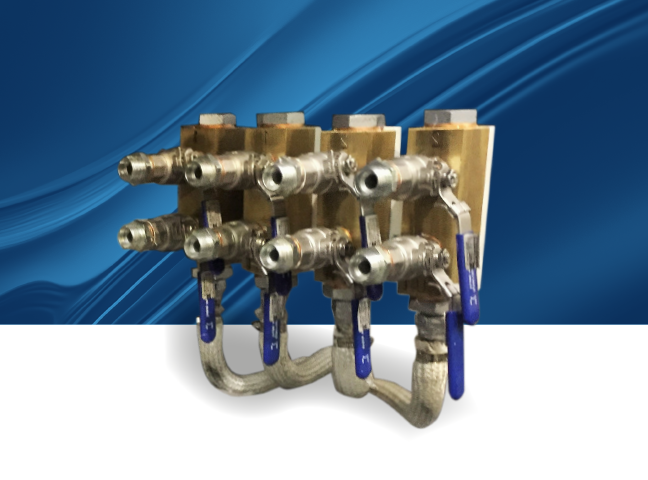
Connection Plants
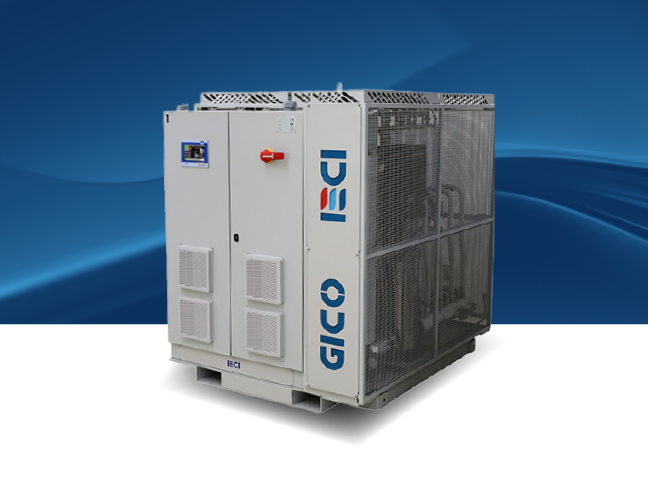
GIGA MEGA Casting
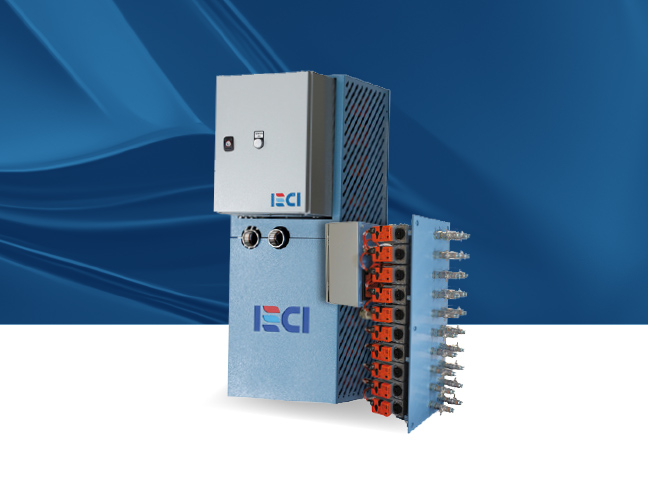
Multi-Cooling
IECI is Worldwide
Not just business partners, but also technical and service centres with 24/7 support.
Exhibitions and events
IECI participates in trade fairs and events in all areas of the world. Die casting, mechanical and foundryevents. Follow us and visit us at our stands.